Plastic extrusion for extra-durable, long-lasting materials
Plastic extrusion for extra-durable, long-lasting materials
Blog Article
A Comprehensive Guide to the Refine and Advantages of Plastic Extrusion
In the substantial realm of production, plastic extrusion emerges as a essential and very effective process. Altering raw plastic right into continual accounts, it caters to a myriad of markets with its exceptional flexibility.
Comprehending the Essentials of Plastic Extrusion
While it might show up complicated at very first glimpse, the procedure of plastic extrusion is essentially simple. The procedure starts with the feeding of plastic product, in the form of powders, pellets, or granules, right into a heated barrel. The designed plastic is then cooled down, solidified, and reduced into preferred lengths, finishing the procedure.
The Technical Process of Plastic Extrusion Explained
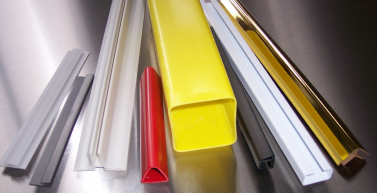
Kinds of Plastic Suitable for Extrusion
The choice of the right sort of plastic is a crucial element of the extrusion process. Different plastics use unique residential or commercial properties, making them much more matched to particular applications. Polyethylene, for instance, is typically utilized due to its low cost and simple formability. It provides exceptional resistance to chemicals and wetness, making it ideal for items like tubing and containers. In a similar way, polypropylene is one more prominent choice as a result of its high melting point and resistance to tiredness. For even more robust applications, polystyrene and PVC (polyvinyl chloride) are usually chosen for their strength and longevity. These are common options, the selection ultimately depends on the details requirements of the item being produced. So, recognizing these plastic types can dramatically boost the extrusion process.
Comparing Plastic Extrusion to Various Other Plastic Forming Approaches
Understanding the types of plastic suitable for extrusion leads the way for a broader conversation on how plastic extrusion compares to other plastic developing techniques. These consist of injection molding, blow molding, and thermoforming. Each technique has its unique uses and benefits. Shot molding, for instance, is excellent for producing elaborate parts, while blow molding is ideal for hollow things like bottles. Thermoforming excels at forming big or shallow components. Nevertheless, plastic extrusion is unparalleled when it concerns creating continuous accounts, like this such as seals, pipelines, and gaskets. It also permits a regular cross-section along the length of the item. Hence, the choice of approach largely depends upon the end-product needs and requirements.
Key Benefits of Plastic Extrusion in Manufacturing
In the world of production, plastic extrusion provides numerous significant advantages. One noteworthy benefit is the cost-effectiveness of the procedure, that makes it an economically attractive manufacturing technique. Additionally, this method provides superior item versatility and improved manufacturing rate, therefore increasing general manufacturing effectiveness.
Cost-Effective Production Approach
Plastic extrusion jumps to the center as an affordable production method in production. In addition, plastic extrusion requires less power than typical production techniques, adding to lower operational expenses. Overall, the economic benefits make plastic extrusion a very attractive option in the manufacturing market.

Superior Item Flexibility
Past the cost-effectiveness of plastic extrusion, an additional significant benefit in making lies in its remarkable product adaptability. This process permits the development of a wide variety of products with differing layouts, forms, and dimensions, from basic plastic sheets to detailed accounts. The flexibility is attributed to the extrusion die, which can be customized to produce the preferred product style. This makes plastic extrusion a perfect remedy for industries that call for tailored plastic parts, such as vehicle, construction, and product packaging. The ability to check my source generate varied products is not only useful in conference particular market needs but also in making it possible for producers to explore brand-new product lines with very little capital expense. Basically, plastic extrusion's product versatility promotes innovation while boosting functional performance.
Improved Production Rate
A considerable advantage of plastic extrusion lies in its improved manufacturing speed. Few other manufacturing procedures can match the speed of plastic extrusion. Furthermore, the capability to maintain consistent high-speed manufacturing without compromising product high quality sets plastic extrusion click now apart from various other approaches.
Real-world Applications and Effects of Plastic Extrusion
In the realm of manufacturing, the strategy of plastic extrusion holds profound significance. This procedure is commonly used in the production of a range of products, such as plastic tubes, home window frameworks, and weather removing. Therefore, it greatly affects markets like construction, packaging, and automobile sectors. Its effect extends to everyday products, from plastic bags to tooth brushes and disposable flatware. The economic benefit of plastic extrusion, primarily its high-volume and cost-efficient result, has actually changed production. Nonetheless, the environmental effect of plastic waste continues to be a problem. The market is persistently striving for developments in recyclable and biodegradable materials, showing a future where the advantages of plastic extrusion can be retained without endangering ecological sustainability.
Conclusion
Finally, plastic extrusion is a effective and very efficient method of changing basic materials right into varied products. It provides many advantages over various other plastic forming techniques, including cost-effectiveness, high output, minimal waste, and design flexibility. Its effect is exceptionally really felt in numerous sectors such as construction, automotive, and durable goods, making it a critical process in today's manufacturing landscape.
Delving much deeper right into the technical procedure of plastic extrusion, it starts with the selection of the appropriate plastic product. As soon as cooled down, the plastic is reduced into the required sizes or wound onto reels if the product is a plastic film or sheet - plastic extrusion. Contrasting Plastic Extrusion to Other Plastic Forming Approaches
Recognizing the types of plastic appropriate for extrusion leads the method for a wider discussion on exactly how plastic extrusion piles up versus other plastic developing techniques. Couple of other production processes can match the rate of plastic extrusion.
Report this page